Quality Management System
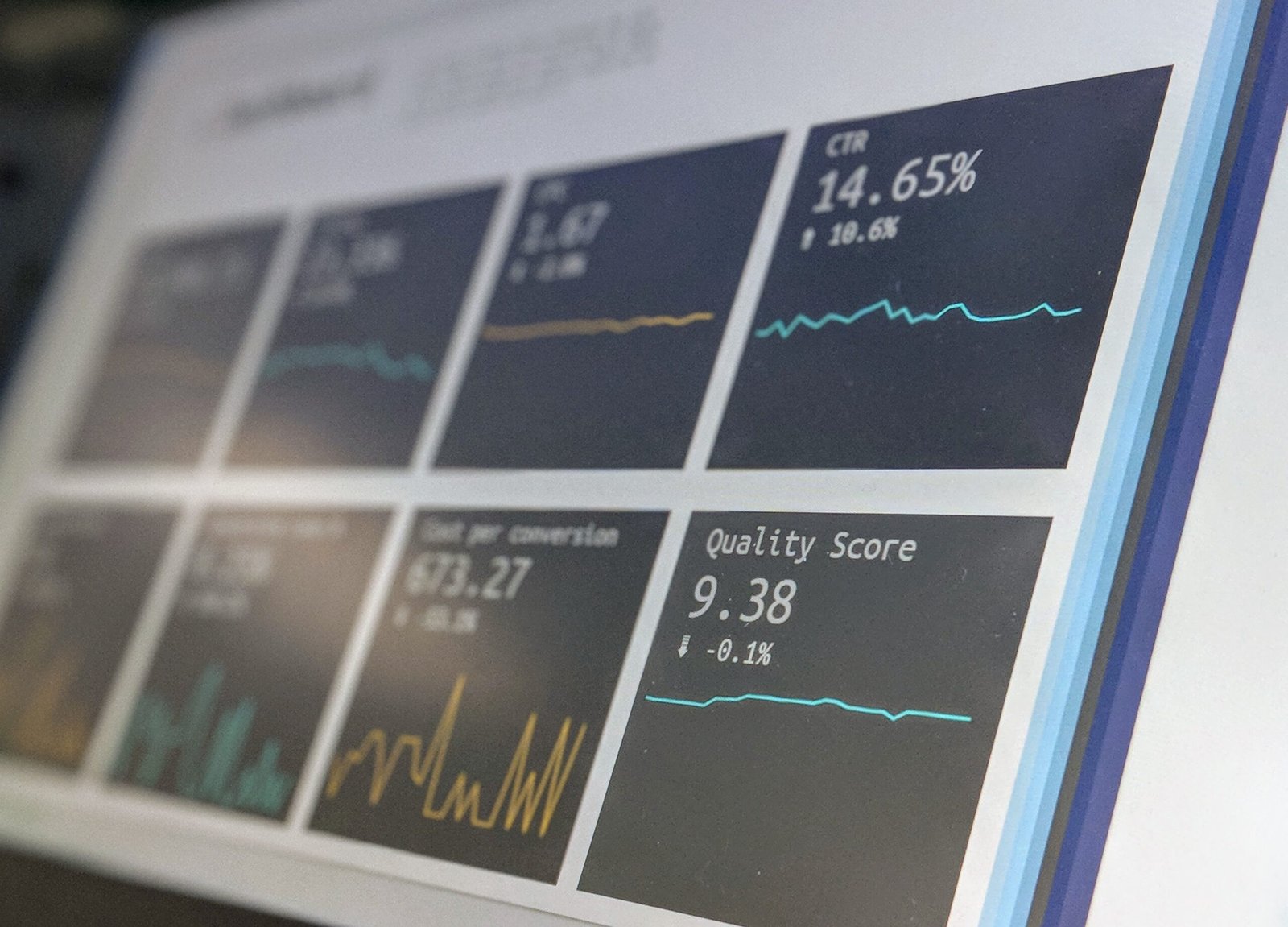
It’s not important how many good products were delivered—only the bad ones count. Quality Management Systems (QMS) enable manufacturers to electronically monitor, manage and document their quality processes to help ensure that products are manufactured within tolerance, comply with all applicable standards, and do not contain defects. QMS provides the procedures, processes, structure, and resources needed to streamline manufacturing and ERP operations while cost-effectively managing quality issues.
Capabilities of QMS
- Define the required quality checks, frequency and sample size.
- Directly capture production parameters from the machines for each produced output.
- First produced product / set-up approvals across manufacturing stages.
- Raw Material qualification and inspection results and provide approval for generating GRN.
- Integrate the lab results with the Production Order (PO) and post to ERP.
- Enforcement of process to ensure compliance.
- Centralized capturing of all shop floor quality data.
- Event monitoring and early trend escalation.
- Intelligent root-cause analysis.
Benefits
- Ensure compliance with organizational and governmental regulations.
- Quality reports automatically attached to every Production Order (PO).
- Easily identify root-cause of quality issues.
- Proactively identify degrading quality of output from machines.
- Shift from problem detection to problem prevention.
- Reduction in cost of quality operations.
Process Monitoring
Process monitoring helps to protect the machine and tools from excessive damage, thereby reducing operating costs and increasing machine uptime. The appropriate process parameters, such as temperature, pressure, flow, vibration and moisture can be collected directly from the machine’s controller (PLC/CNC), if provided by the OEM as part of the machine. If not, we would need to place appropriate sensors or devices that measures the required parameters. The trend of the parameters can be measured against an ideal “golden” scenario to understand the machine performance and tool degradation.
Benefits
- Generates alerts and alarms when parameters move outside the specification limits.
- Achieve in-process quality control by monitoring critical quality parameters.
- Eliminate faulty production by keeping processes running in their target zone.
- Helps identify root-cause of quality defects.
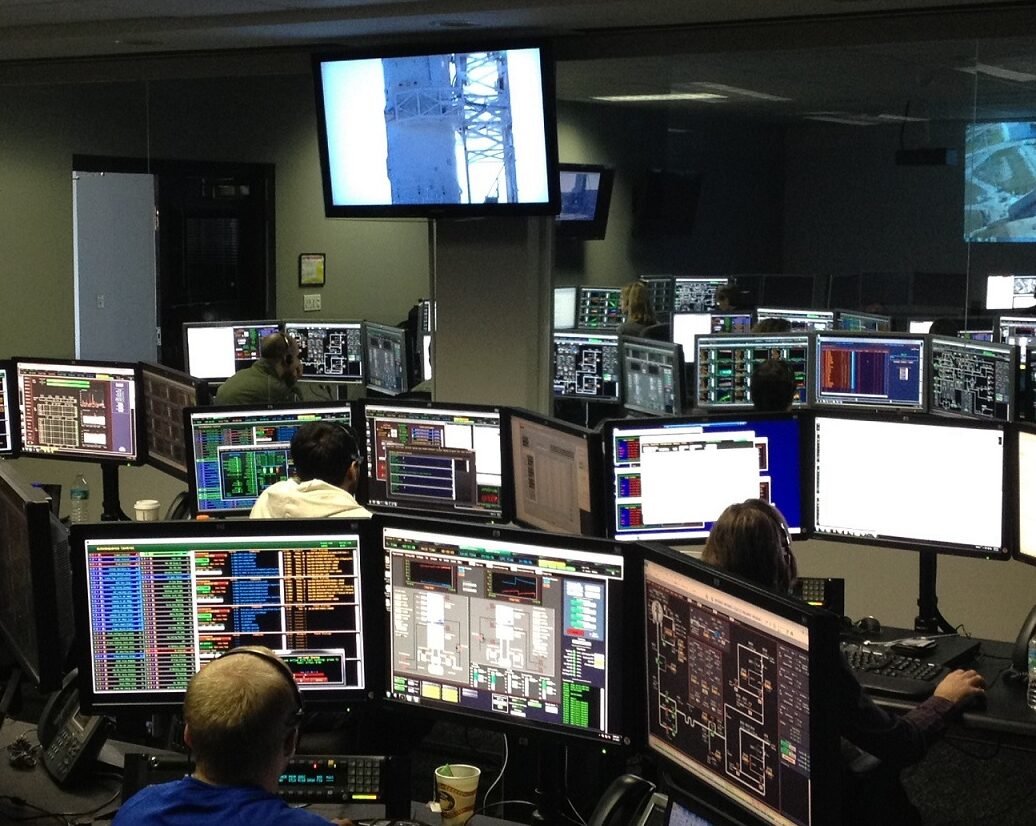
Statistical Process Control (SPC)
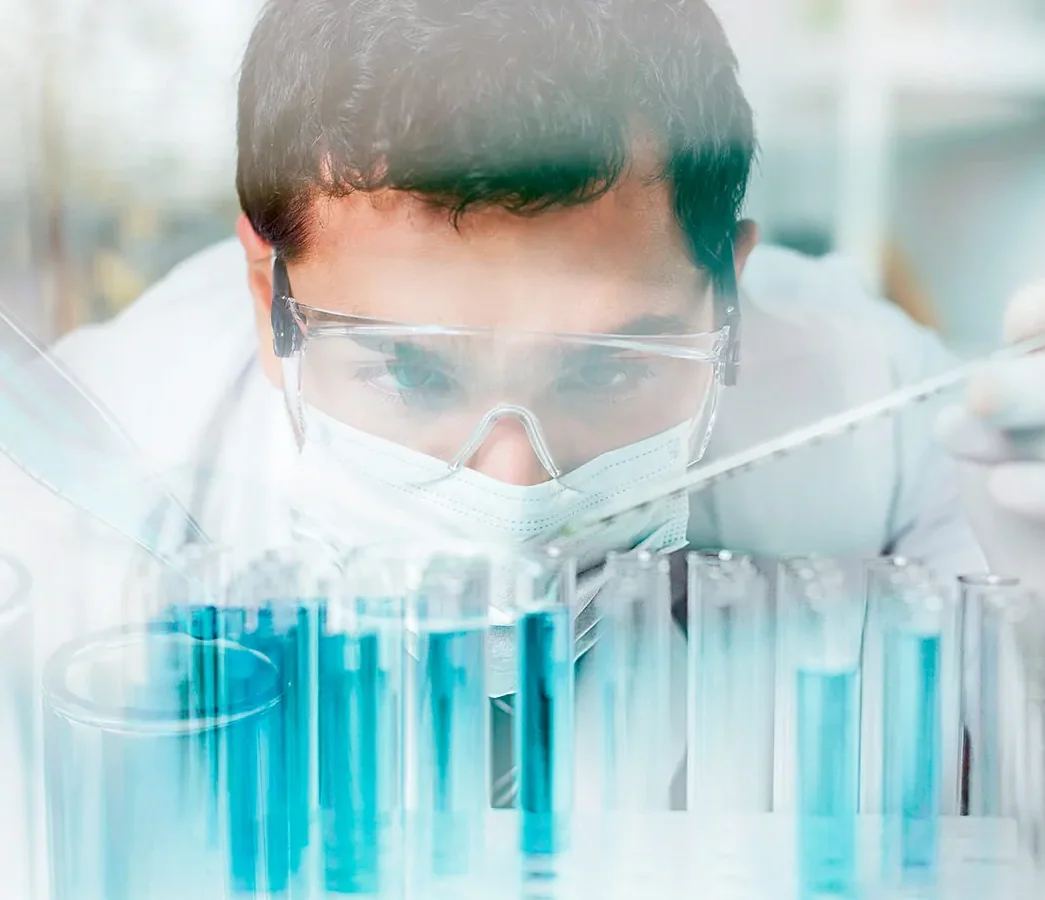
SPC is the use of statistical techniques to control a process or production method. SPC tools and procedures can help you monitor process behavior, discover issues in internal systems, and find solutions for production issues. SPC focuses on minimizing variation in a process and ensure consistent output quality. It is critical that, when SPC provides early-warning of emergent issues, that key personnel on the manufacturing line are alerted and can take appropriate action to resolve the issue and prevent the nascent problem from being a line-stopping problem. By moving the responsibility on quality inspection more to real-time, SPC can help catch issues as they are emerging, instead of after they have occurred.
Benefits
- Catch undesired process variations as they occur and proactively reduce rework, scrap and rejections.
- Improve quality by gaining an in-depth understanding of the process parameters.
- Improve the process by analyzing the data and understanding the sources of process variations.
- Reduce manual quality inspections.
- Extensive analytics and reporting.
Vendor Performance
The quality of your raw materials relates to the performance of your manufacturing process. So, it is important to maintain a supplier non-conformance management system, which can help you benchmark your suppliers and drive them to deliver better quality of materials.
- Build a performance history of your suppliers by tagging the recorded lab results and quality checks of each order.
- Easily compare the performance of multiple suppliers supplying similar materials.
- Assess the performance of the materials supplied by prospective suppliers for testing purposes, and compare their material performance with those of existing suppliers.
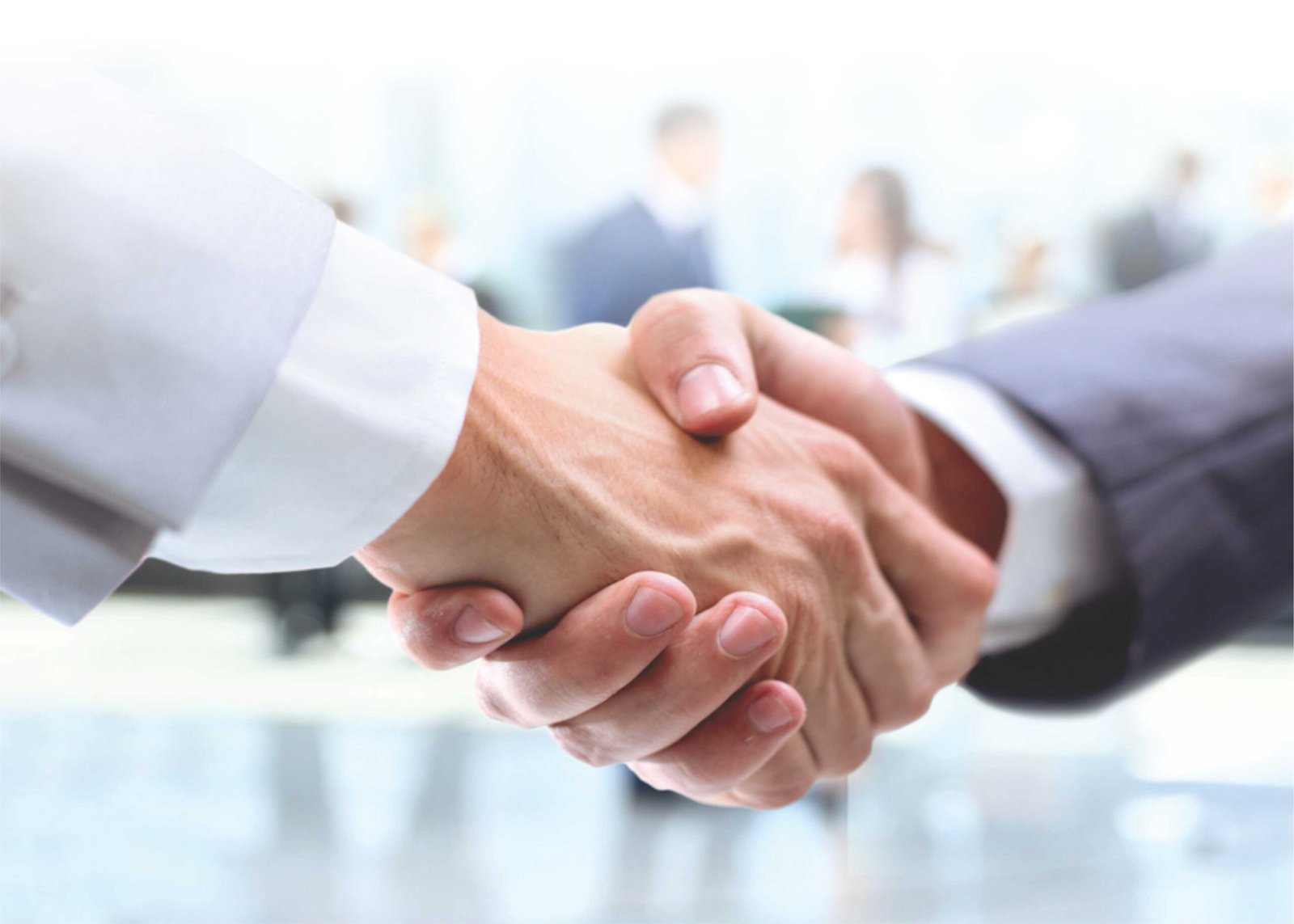